El mantenimiento predictivo se ha convertido en un pilar fundamental para la gestión eficiente de equipos e infraestructuras en industrias como la minería y la manufactura. Una de las técnicas más efectivas en el planeamiento de mantenimiento es la termografía, una herramienta que permite identificar fallos potenciales antes de que se conviertan en problemas críticos. Este artículo profundiza en las ventajas de la termografía para la prevención de fallos y su papel en el mantenimiento predictivo, centrándose en su impacto en la reducción de costos y la optimización de presupuestos.
Tabla de contenidos
¿Qué es el Mantenimiento Predictivo?
El mantenimiento predictivo es una estrategia de gestión de mantenimiento que se basa en la monitorización continua del estado de los equipos para prever y prevenir fallos. A diferencia del mantenimiento correctivo, que repara los equipos solo después de una falla, y del mantenimiento preventivo, que sigue un calendario fijo de revisiones, el mantenimiento predictivo utiliza datos en tiempo real para intervenir solo cuando es necesario.
Principales Técnicas de Mantenimiento Predictivo
1. Análisis de vibraciones: Evalúa las vibraciones de los equipos para detectar desajustes, desgastes y problemas de balanceo.
2. Termografía Infrarroja: Detecta anomalías térmicas en componentes eléctricos y mecánicos, lo que permite identificar problemas antes de que sean visibles a simple vista.
3. Análisis de Aceite: Examina el estado del lubricante y la presencia de partículas metálicas, lo que indica el desgaste interno de las máquinas.
4. Ultrasonido: Identifica fugas de aire, gas y problemas en componentes eléctricos mediante ondas ultrasónicas.

La Termografía en el Planeamiento de Mantenimiento
La termografía es una técnica no invasiva que utiliza cámaras infrarrojas para medir la temperatura de los componentes y equipos en funcionamiento. Esta tecnología permite identificar puntos calientes y fríos que pueden indicar problemas como sobrecalentamiento, desgaste de rodamientos, conexiones eléctricas defectuosas y obstrucciones en sistemas de refrigeración.
Funcionamiento de la Termografía
La termografía se basa en la detección de radiación infrarroja emitida por los objetos. Al medir estas emisiones, las cámaras termográficas generan imágenes en tiempo real que muestran las temperaturas superficiales de los equipos. Las áreas con temperaturas anómalas se resaltan en colores, lo que facilita la identificación de fallas potenciales.
Aplicaciones de la Termografía en la Industria
1. Motores y Generadores: Detección de puntos calientes que indican problemas de aislamiento o sobrecarga.
2. Tableros Eléctricos: Identificación de conexiones sueltas, sobrecalentamiento de interruptores y fusibles defectuosos.
3. Rodamientos y Ejes: Localización de puntos de fricción que pueden provocar desgaste prematuro y fallos mecánicos.
4. Sistemas de Refrigeración: Detección de obstrucciones o fugas que afectan el rendimiento del sistema.
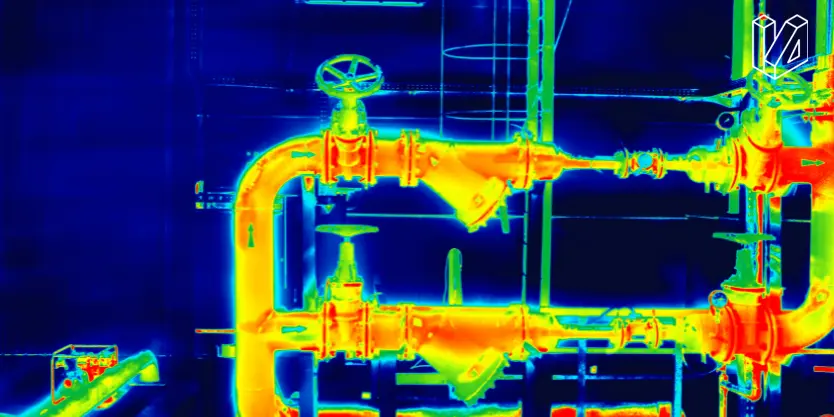
Ventajas de la Termografía en el Mantenimiento Predictivo
La termografía ofrece múltiples beneficios en el mantenimiento predictivo, especialmente en entornos industriales complejos como minas y fábricas, donde la prevención de fallos es crucial para la continuidad operativa.
Reducción de Costos y Optimización de Presupuestos
1. Prevención de Fallos Catastróficos: La identificación temprana de problemas mediante termografía evita paradas inesperadas de los equipos, reduciendo así los costos asociados a reparaciones de emergencia y pérdidas de producción.
2. Extensión de la Vida Útil de los Equipos: Al detectar y corregir fallos menores antes de que se conviertan en problemas graves, se prolonga la vida útil de los activos, optimizando los presupuestos de mantenimiento.
3. Reducción de Costos Energéticos: La termografía ayuda a identificar puntos de pérdida de energía, como aislamiento térmico deficiente y equipos sobrecalentados, lo que permite corregir problemas y mejorar la eficiencia energética.
Mejora en la Seguridad de la Operación
1. Detección de Riesgos Eléctricos: Las inspecciones termográficas permiten detectar puntos de sobrecalentamiento en sistemas eléctricos que podrían causar incendios o fallos graves.
2. Menos Intervenciones No Programadas: Al reducir la necesidad de mantenimiento correctivo, se disminuye la exposición del personal a entornos peligrosos, mejorando así la seguridad laboral.
3. Mantenimiento sin Interrupciones: La termografía permite realizar inspecciones sin detener la operación, minimizando los tiempos de inactividad y mejorando la eficiencia.
Eficiencia en la Gestión del Mantenimiento
1. Planificación Basada en Datos: La termografía proporciona datos precisos sobre el estado de los equipos, permitiendo una planificación de mantenimiento basada en la condición real de los activos, en lugar de basarse en suposiciones o cronogramas fijos.
2. Mantenimiento Prioritario: Permite enfocar los recursos de mantenimiento en los equipos que realmente lo necesitan, optimizando así el uso del presupuesto y los tiempos de intervención.
3. Integración con otras Herramientas de Mantenimiento Predictivo: La termografía se complementa con otras técnicas como el análisis de vibraciones y el ultrasonido, proporcionando un enfoque integral para la gestión del mantenimiento.
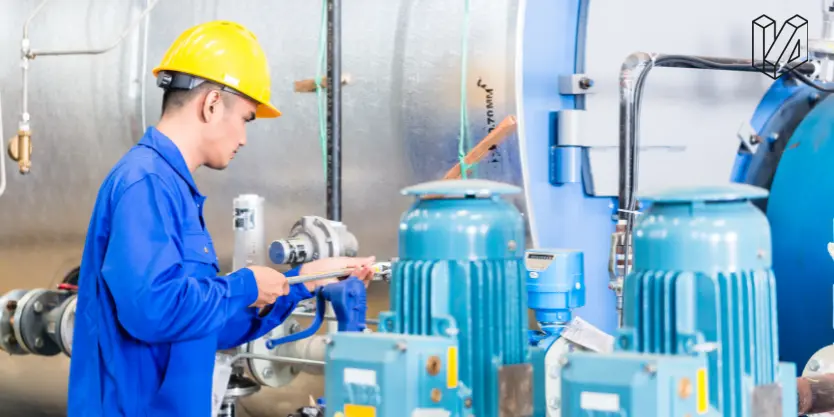
Implementación de la Termografía en el Mantenimiento Predictivo
Pasos para Integrar la Termografía en la Gestión de Mantenimiento
1. Evaluación de Necesidades: Identificar los equipos críticos y los posibles puntos de fallo que pueden beneficiarse del uso de la termografía.
2. Selección de Tecnología: Elegir cámaras termográficas adecuadas, considerando la resolución, rango de temperatura y facilidad de uso.
3. Capacitación del Personal: Formar a los técnicos en la correcta utilización de las cámaras termográficas y la interpretación de los datos.
4. Integración con Sistemas de Gestión: Incorporar los resultados de las inspecciones termográficas en el software de gestión de mantenimiento para planificar intervenciones y ajustes.
5. Monitoreo Continuo y Ajustes: Realizar inspecciones regulares y ajustar las estrategias de mantenimiento basadas en los hallazgos.
Desafíos en la Implementación
1. Costo Inicial: La inversión en equipos de termografía y la capacitación del personal pueden suponer un gasto inicial elevado, aunque se recupera rápidamente con la reducción de fallos y optimización de recursos.
2. Interpretación de Resultados: Requiere personal capacitado que pueda interpretar correctamente los datos para tomar decisiones adecuadas.
3. Integración con otros Sistemas: La termografía debe complementarse con otras herramientas y tecnologías para obtener una visión completa del estado de los equipos.
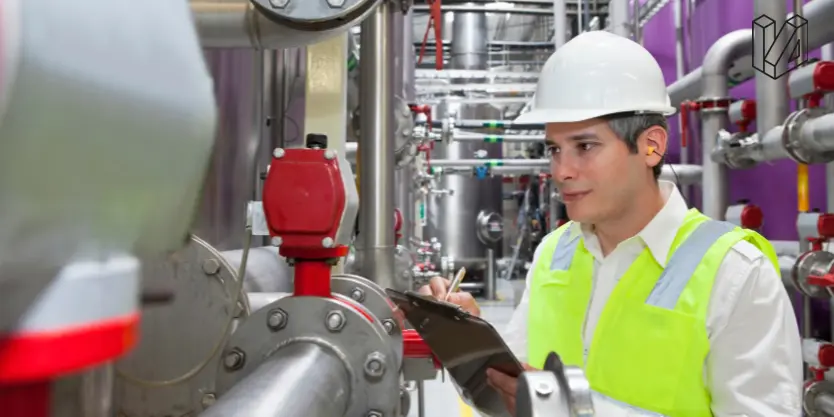
Conclusión: La Termografía como Pilar del Mantenimiento Predictivo
La termografía se ha consolidado como una herramienta esencial en el mantenimiento predictivo, ofreciendo una ventaja significativa en la prevención de fallos y la optimización de costos y presupuestos. Su capacidad para detectar problemas antes de que se conviertan en fallos graves no solo mejora la eficiencia operativa, sino que también extiende la vida útil de los equipos y mejora la seguridad de las operaciones.
En industrias exigentes como la minería y la manufactura, donde la continuidad y la seguridad son vitales, la integración de la termografía en el planeamiento de mantenimiento representa una inversión inteligente. Para ingenieros mecánicos, ingenieros de confiabilidad y encargados de mantenimiento mecánico, la adopción de esta tecnología no solo proporciona un enfoque proactivo para la gestión de activos, sino que también redefine los estándares de excelencia en la gestión de mantenimiento.
La termografía, combinada con otras técnicas predictivas, ofrece un enfoque integral para la gestión de activos, permitiendo a las empresas reducir costos, mejorar la seguridad y maximizar la eficiencia operativa. Para los profesionales encargados de la gestión del mantenimiento, esta tecnología representa una herramienta invaluable para alcanzar los más altos niveles de rendimiento y sostenibilidad en la industria.